Minneapolis-based writer Julie Kendrick tours Red Wing Shoes’ century-old factory to understand how the American icon blends tried and true with the new — techniques, machinery and even craftspeople — to make 16,000 pairs of work boots every week.
Based on the way most of us behave, it would be easy to conclude that we humans are merely a pair of thumbs and a set of screen-fixated eyes. But we’ve got feet, too — humble, hard-working, often overlooked feet. And those feet need to be kept safe and comfortable, especially for people who work at some of the world’s toughest jobs.
Since 1905, Minnesota’s Red Wing Shoe Company has provided tough work boots to farmers, construction workers, service technicians and anyone else who counts on rugged footwear to help them get the job done. Four generations of shoemakers have worked at Red Wing. Today, 400 employees turn out 16,000 pairs of handcrafted boots every week from the company’s factory on the banks of the Mississippi River in Red Wing, Minn.
One of the guardians of this iconic brand is Roy Smith, a 44-year Red Wing employee and the company’s technical director. Smith oversees operations at the factory, from staffing and new-employee training to manufacturing processes and even new-leather assessment.
He carries himself with a military bearing, and his blue eyes are in constant motion while surveying the many individual work stations on the bustling factory floor. Smith explains that the factory uses a blend of what he calls “old school” and automated technologies. He shows me computerized leather-cutting machines imported from Italy set up next to stitching machines from the turn of the 20th century.
“It’s a balance now [between hand work and automation],” Smith says. “Many parts of the shoemaking process require a critical eye, and a machine can’t always do that. But as some of our senior shoe cutters retire, for example, we need to be aware of the learning curve, and we need to make sure we still get the results we need.”
The Heart and Soul of Red Wing
The Red Wing story can’t be told without mention of Puritan Stitch machines, each of which bears a brass plaque with its patent date: January 31, 1893. It’s tempting to say that they don’t make them like that anymore, but it turns out that machines are still produced by Puritan Industries, headquartered in Collinsville, Conn. The Puritan makes a chain stitch, which means the thread is double looped, with one loop threading through the other.
“It’s like the stitch you find on a bag of dog food or charcoal briquettes,” Smith says.
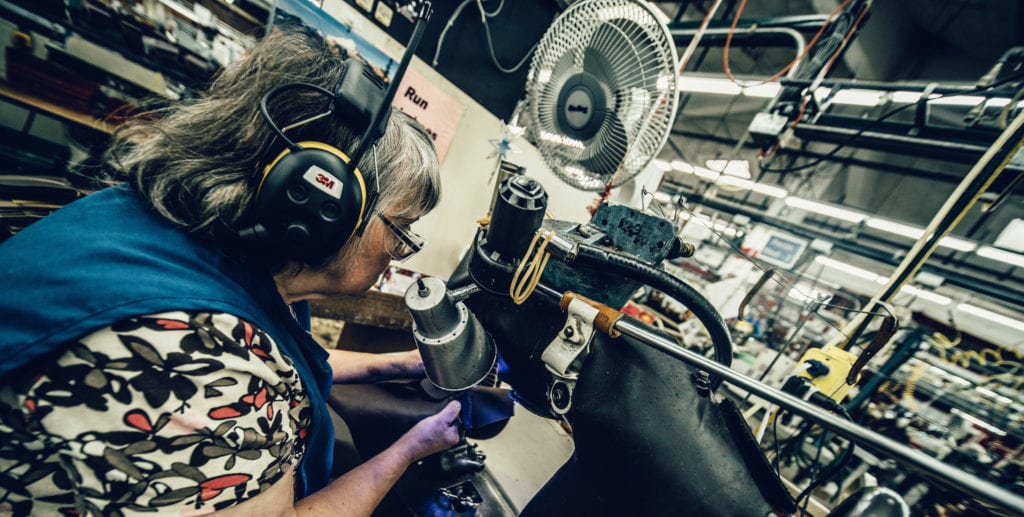
A Puritan Stitch machine making a triple-stitched seam. Melted wax acts as a lubricant as it passes through the needles and leather. As the thread dries, it seals the stitch and prevents fraying. Image: Red Wing Shoe Company, Inc.
Some time ago, before Smith joined Red Wing in 1974, someone fitted leather covers over the Puritan machines. The covers look like miniature saddles for ancient, durable workhorses. And they’re necessary: The Puritans are loud, and when a machine is running well, Smith says, it sounds like a machine gun firing off.
It’s rare for a machine like the Puritan to still be in production, 126 years after its patent was issued. It’s rarer still to find a technician skilled enough to fix them.
“The guy who sold and worked on them was named Ray Burnside, and he’d swing by every couple years,” recalls employee Dave Van Houten. “He went all over the world for these machines, and, boy, did he have some stories. He knew them so well. He could just listen to them running and tell you if they were too dry, or if they were about to need repair. When a cam gets hot and there’s no oil on it, it’ll squeal. He could hear it.”
Burnside was famous for his ability to rebuild a Puritan. “He’d break them down, then clean and paint all the castings. He’d soak the cams in oil,” Van Houten says. “He was so old school. He always had one of our mechanics with him so his knowledge could be handed down.”
When Burnside died five years ago, Van Houten says there was a panic at Red Wing: “We wondered what we’d do without him.” But then Burnside’s wife, Irene, contacted the factory to say that she intended to keep up the independent parts and service business. “So we buy our parts from Irene now,” Van Houten says.
Artisans Work the Leather Alongside High-Tech Machinery
One area in which handcrafting and automation work side by side is hide evaluation and leather cutting. Leif Dunlap sorts leather for use in various shoe components. The best leather makes up the vamp, the part that you see when you look down at your shoes. As we talk, it’s clear that Dunlap, an eight-year employee, brings an artisan’s knowledge to his work. He runs his hands in wide strokes over the entire hide and shows me a handheld gauge that measures the hide’s thickness. “The gauge just verifies what I already know. I usually just feel it with my hands.”
“That’s the kind of passion you see in a lot of people who work here,” says Smith, as we leave Dunlap’s work station.

Leif Dunlap, left, sorts and grades leather hides; right, he checks the thickness of the leather in different sections of the hide. Images: Julie Kendrick
There’s been significant retirement-fueled turnover in the past five years, and Smith estimates that now about 40 percent of the workforce has been at Red Wing for 40 years or more. The rest have much shorter tenures. He acknowledges that finding and retaining qualified employees is an ongoing challenge. “It’s hard to find good employees. But that’s not just this industry, that’s any industry. People have so many options.”
As I walk the factory floor, it’s clear that older workers are making way for a younger crowd. Young people with beards and tattooed arms work alongside silver-haired veterans who started at Red Wing right out of high school in the ’70s or ’80s.
In another area of the floor, several employees are using carefully placed dies to cut whole hides into pieces. Leather is the most expensive part of the shoe, says Smith, so it’s important to get the most from every hide. Behind the employees, a computerized machine evaluates a hide, assigning value areas that make the leather resemble a weather map. A separate machine makes cuts based on the data it’s received about the coded hide.
“Many parts of the shoemaking process require a critical eye, and a machine can’t always do that. But as some of our senior shoe cutters retire, for example, we need to be aware of the learning curve, and we need to make sure we still get the results we need.” — Roy Smith, technical director, Red Wing Shoes
The high-tech route is fast and precise, but it does have disadvantages. These automated machines are produced in Italy, and there is only one technician in the entire United States assigned to service them. There’s also a cultural divide.
“The entire country [Italy] shuts down for a month in August,” Smith says, “so when a machine breaks the first of day August — and it happened here — that’s a problem.”
Making the Parts That Make the Machines That Make Red Wing Footwear
Keeping all of this machinery in working order is a daunting task for the onsite team of mechanics. When parts are needed, the team sources some online from specialty retailers and makes others in-house.
“If we can find one good part, then Al Weberg in our machine shop can recreate it,” Van Houten says, noting that the parts need to stand up to the product and the production method.
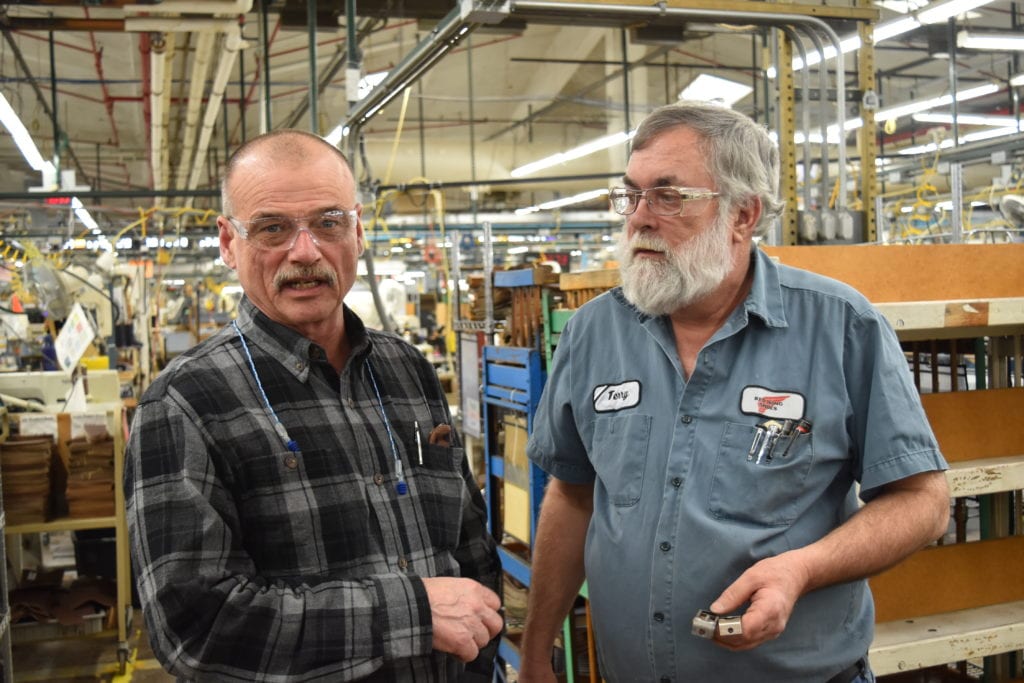
Roy Smith and Terry Amyx, right, who works in Red Wing Shoes’ maintenance department. Image: Julie Kendrick
Van Houten introduces me to Terry Amyx, who works in the maintenance department. He shows me a throat-plate replacement part that’s been produced on a 3D printer, one of his team’s first forays into this technology. He’s hopeful that 3D production can provide more-precise parts.
“We can get brand-new parts and put them on old machines, but it usually requires hand fitting, and that might mean filing, sanding, polishing and buffing,” Amyx says.
When I ask how many machines are on the factory floor right now, Smith, Van Houten and Amyx are initially stumped until finally they decide that “at least a thousand” is a pretty good estimate. There are four file cabinets and two upright cabinets filled with original manuals for those machines.
“But there are still gaps,” Amyx says. “Someone could have lost the manual 30 years ago, and then you’re just having to figure it out for yourself.”
It’s that “figure it out for yourself” work ethic that’s kept the machinery at the Red Wing Shoe Company humming since 1905. Employees like Amyx and Van Houten can overcome the challenge of hard-to-find parts, finicky equipment — and even monthlong Italian holidays — to make reliable shoes for hard-working people.
Share this: