Field service documentation is evolving impressively these days, to say the least. Most tenured technicians can remember a time when a bulky, slow laptop offered up scans of their repair procedures and crude, non-scalable images of parts lists. And a few senior technicians (including yours truly) have not-so-fond memories of dirty, torn paper manuals that took up half the space in their service trucks. Today’s electronic documents (or e-docs) are so advanced that they nearly fix the machines by themselves and can exist as apps on technicians’ smartphones.
The Army’s E-Doc Frontlines
For a prime example of how far we’ve come in improving e-docs, look no further than the Army’s new Interactive Electronic Technical Manual (IETM) for the Spider XM7 Network Munition Dispensing Set.
A field service repair manual for a hand-emplaced, remote munitions system, the IETM does much more than provide adjustment specs, parts lists and troubleshooting procedures. Its 3D scalable graphics allow soldiers who are performing a repair to “grab hold” of a component, spin it around for a different view and zoom in for a closer look.
Any technician who has performed a complex repair on an unfamiliar machine knows that when a manual tells you to “remove the four screws securing the motor to the housing — see figure A,” but then warns “do not remove the two screws securing the solenoid or you will need a new assembly,“ the ability to zoom in and rotate the graphic to ensure that you’re looking at the right screws can save a lot of frustration — and maybe even a little money.
A Virtual Trainer in the Field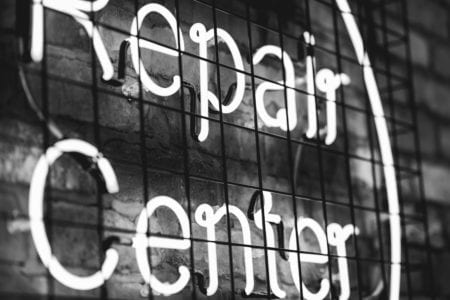
E-docs are now more than databases of searchable information; they have become virtual trainers as well. IETM users can watch a video of the repair and take a quiz in which they virtually perform the procedure before attempting it on an actual machine. If they make a mistake, they receive an error message and can try it again. I imagine that some real-life missteps in repairing actual war machinery would be less forgiving.
Some repair e-docs incorporate diagnostic procedures where the repair person interfaces directly with the machine in question, usually via a cable or WiFI. A tech will not be able to proceed to the next step without this interaction, thus leaving a data trail that shows the procedure has been followed correctly.
Even though the vast majority of field service repair mistakes never lead to personal injury or destruction, many techs still must learn by doing trial-and-error repairs onsite. Service reps will often go through months of training on a new product before they ever see one in the field. Unless they all have photographic memories, some of what they learned will be lost and mistakes will be made — sometimes expensive mistakes. Virtual training on e-docs can save the accumulated costs of trial-and-error mistakes by novice technicians in the field.
How Technicians Are Improving E-Docs
A seldom discussed aspect of electronic documentation is how technicians contribute to its power and flexibility, both actively and passively. Techs actively improve e-docs when a company solicits, closely monitors and incorporates their feedback. Some companies even reward techs who submit time- or money-saving ideas on how to improve their electronic documentation.
Even without giving direct feedback, technicians passively improve e-docs when companies mine data on their use of them. By merging troubleshooting procedures with diagnostic procedures, businesses can track if technicians are following instructions on repairs. They can even monitor the time a repair takes from its start to its completion. (This passive input by technicians should be taken with a grain of salt, as service reps will inevitably memorize a procedure or repair and only boot up their computers when it’s time to run the diagnostic.)
Are the sometimes costly innovations in electronic documentation worth it? From my perspective, the answer is clear. Whether it’s a soldier on the battlefield ensuring the safe operation of a munitions system or a newly trained refrigeration technician preventing mass spoilage at a supermarket, the benefits that interactive 3D graphics and virtual training add to service documentation are priceless.
Share this: