By embracing 3D printing, General Electric is disrupting not only manufacturing, but also paving the way for major changes in the service industry.
Editor’s note: This story first appeared in the latest issue of Field Service, a quarterly print magazine from Field Service Digital and ServiceMax. Check out the full magazine in print or online.
About 10 years ago, the GE’s aviation division set out to create a new, one-of-a-kind engine, one that incorporated an advanced fuel nozzle. The fuel nozzle is a critical component for fuel burn and emissions, but GE had a problem: Manufacturing the nozzle from the planned design was going to be difficult and time-consuming using traditional methods.
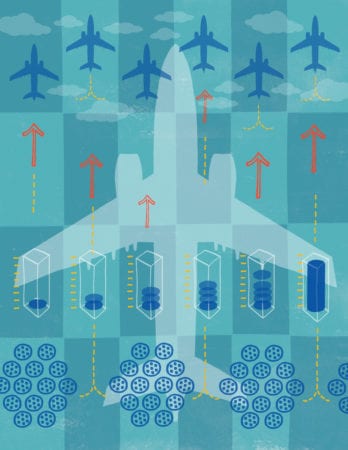
Illustration by Leigh Wells
So GE embarked on a partnership with Greg Morris, co-founder of Cincinnati-based Morris Technologies, to “print” the nozzle. By 2012, each of the 19 fuel nozzles in every LEAP aircraft engine was produced using 3D printing, an additive manufacturing process that layers and sinters composite materials to make a three-dimensional object. Today the LEAP engine, made by a company jointly owned by GE and France’s Safran Aircraft Engines, is GE’s best-selling jet engine, with more than 11,500 engines valued at $80 billion on back order, and hundreds more going into service this year on Boeing 737 airplanes.
Manufacturing is already being disrupted by 3D printing. Next up? The service industry. With newer materials and faster 3D printers, it’s not far-fetched to envision technicians at various work sites printing parts on demand for wind turbines, oil-drilling equipment or even replacement parts for jet engines.
Going All In on 3D Printing
In 2012, GE acquired Morris Technologies to help prepare for a 3D-printed future. Three years later, in 2015, GE opened the Additive Development Center, a $140 million project based in Cincinnati, where GE Aviation is also headquartered. That same year, GE spent $50 million to upgrade its plant in Auburn, Ala., with industrial-sized 3D printers to mass produce the LEAP engine fuel nozzles.
“This technology is just fundamentally disruptive. It’s changing the way we think about how a product gets designed,” says Morris, now business development manager of additive technologies at GE Aviation. “Why stop at the fuel nozzle? Why not make more parts?”
GE’s push into additive technologies is rapidly expanding beyond fuel nozzles. In April 2016, GE opened its $40 million Center for Additive Technology Advancement outside Pittsburgh, Penn., where 50 workers are teaching and training employees across company divisions how to use industrial 3D printers and incorporate 3D-printing technology into their own projects. GE’s Oil & Gas division is already using 3D printing to make valves. GE Power could one day use industrial printers to make parts for wind turbines.
There’s a push to train designers and engineers across the company to approach product design with 3D printing in mind, Morris says. “How do you design with this technology? What are the pros and cons? We’ve certainly been trying to get other people involved in how to work with the technology in all the GE businesses,” Morris says.
For GE, the advantages are twofold: cost savings and manufacturing innovation. By the end of this decade, GE Aviation expects to manufacture more than 100,000 parts for the LEAP and other engines using additive manufacturing, and the company overall is on a kick to become a leader in the additive sector.
Investing in a 3D-Printed Tomorrow
So far since 2010, GE has invested $1.5 billion in 3D printing by acquiring companies like Morris Technologies, establishing new manufacturing facilities and training employees. The company took another big step last September when it spent $1.4 billion to acquire two European firms: Sweden’s Arcam AB and Germany’s SLM Solutions Group, both of which have experience in the aerospace and healthcare industries.
GE expects that both companies will improve the service side of its business by cutting customer costs on maintenance. The 3D-printing process enables the rapid creation of new and spare parts, which in turn drops costs for GE and the customer.
The latest round of acquisitions also foreshadows where GE expects to be in the additive manufacturing sector 10 years from now.
“We need to be vertically integrated into this space, and we need to make this one of the GE businesses — meaning GE Additive will become one of the GE vertical businesses at some point,” Morris says.
By 2026, Morris says GE wants to be “the largest player” in the additive manufacturing sector, both in terms of selling machines and equipment and providing third-party companies new to 3D printing the engineering and design talent to get them off the ground. In other words, small and midsize businesses interested in using 3D printing can head to GE Additive to buy industrial 3D printers and the necessary materials, as well as hire GE-trained, specialized technicians to demonstrate how to integrate and use 3D printers for their own business needs.
That’s the future for GE, and it’s one that will only accelerate, according to Morris, as new materials and faster 3D printers allow for the printing of larger, more durable parts. With GE Additive, the company hopes to lead the charge.
“We even want to sell to the competitors. We want to sell to Rolls-Royce, Philips, Honeywell and more,” Morris says. “As GE Additive, we plan to sell to the world.”
Share this: